Flange connection is composed of flange, gasket, bolt and nut connection. It is a detachable connection that can be used to connect pipes and valves, pipes and pipes, and pipes and equipment. The flange connection not only has the flexibility of installation and disassembly, but also has reliable sealing performance, high strength, simple structure, low cost, and can be repeatedly disassembled. Because the flange has good comprehensive performance, it is widely used in basic projects such as chemical industry, construction, water supply, drainage, petroleum, light and heavy industry, refrigeration, sanitation, plumbing, fire fighting, electric power, aerospace, shipbuilding and so on.
01 Classified by connection method
Flanges can be divided into integral flanges, flat welding flanges, butt welding flanges, loose flanges and threaded flanges according to the connection mode.
Integral flange refers to the inlet and outlet flanges that connect pumps, valves, machines and other mechanical equipment with pipelines. They are usually integrated with these pipeline equipment as a part of the equipment.
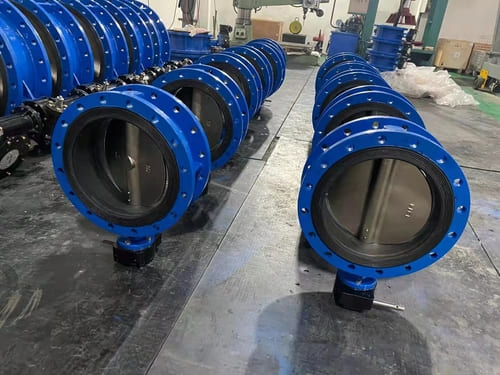
Flat welding flanges are also called lap welding flanges. When the flat welding flange is fixed to the pipe, the end of the pipe is inserted into the bottom of the flange socket or the inner flange of the flange, and is lower than the inner plane of the flange, and the outer flange or inner and outer flanges are welded to make the flange Connect with the pipeline. Its advantages are that it is easier to center during welding and assembly, and the price is cheap, so it has been widely used. Flat welding flanges are only suitable for piping systems where the pressure level is relatively low, and pressure fluctuations, vibrations and shocks are not serious.
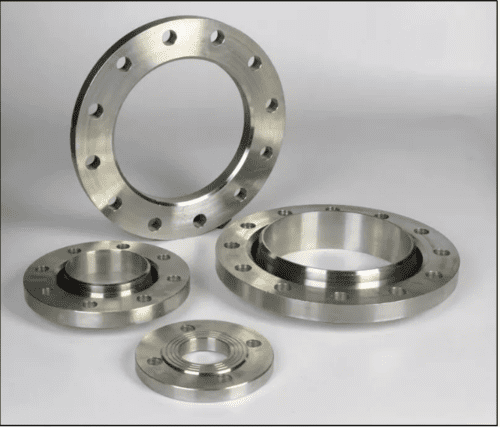
Butt welding flange is also called high neck flange. It is different from other flanges in that there is a long and inclined high neck from the welding point of the flange and the pipe to the flange. The wall thickness of this high neck gradually transitions to the thickness of the pipe wall along the height direction, which improves the stress resistance. Continuity, thus increasing the strength of the flange. Butt-welded flanges are mainly used in occasions with harsh working conditions (such as pipeline thermal expansion or other loads that cause greater stress on the flange) or occasions where stress changes are repeated, as well as pipelines with large fluctuations in pressure and temperature, and high temperature and high pressure. And sub-zero temperature pipelines.
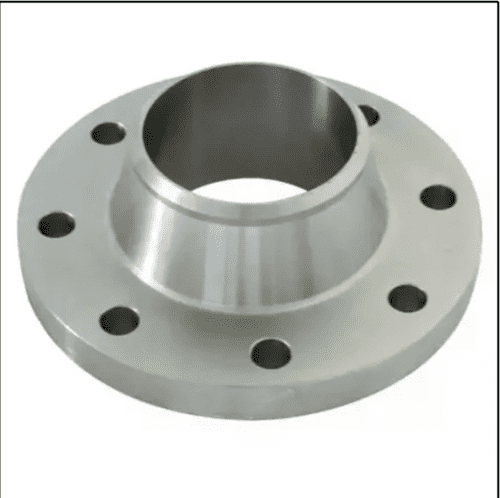
Loose flanges are commonly known as loose flanges. They are divided into welded ring loose flanges, flanged loose flanges and butt welded loose flanges. They are mostly used on copper, aluminum and other non-ferrous metals and stainless steel pipelines. The connection of loose flanges is actually achieved by welding, but this flange is loosely sleeved on the accessory components that have been welded together on the pipe, and then the accessory components and gaskets are compressed by connecting bolts to achieve sealing. Lan (ie loose sleeve) itself does not contact the medium. The advantage of this flange connection is that the flange can be rotated, the bolt hole is easy to center, and it is easy to install on large-diameter pipelines, and it is also suitable for places where the pipeline needs to be frequently removed for cleaning and inspection. The material of the flange accessory components is the same as that of the pipe, but the material of the flange can be different from that of the pipe (the flange material is mostly Q235, Q255 carbon steel), so it is more suitable for pipelines that transport corrosive media. However, the pressure resistance of loose flanges is not high, and it is generally only suitable for the connection of low-pressure pipelines.

Threaded flange is a kind of non-welded flange by processing the inner hole of the flange into pipe thread, and cooperate with the pipe with external thread to realize the connection. Compared with welding flanges, it has the characteristics of convenient installation and maintenance. It can be used in some scenes where welding is not allowed. However, it is recommended not to use threaded flanges under the conditions of higher than 260°C and lower than -45°C. , So as to avoid leakage.
Nominal diameter of threaded flange: DN8~DN100 Working pressure: 1.0~2.5 (MPa).
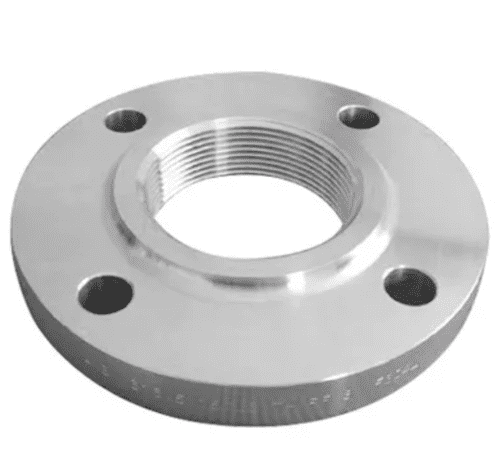
02 Classified according to the form of sealing surface
The sealing surface of the flange is mainly selected according to the process conditions, the sealing diameter and the gasket.
The sealing surface of the container flange has flat surface, concave-convex surface, tongue-and-groove surface, etc. Among them, concave-convex surface and tongue-and-groove surface are the most commonly used.
There are six types of pipe flange sealing surface: full plane, raised surface, concave and convex surface, tongue and groove surface, O-ring surface and ring connection surface. See Table 1 for the form and code of the flange sealing surface.

The plane type is to process a few shallow grooves on the plane, and its structure is simple, but the coupon is not fixed and it is not easy to compress. Suitable for occasions where the pressure is not high and the medium is non-toxic.
The convex type is similar to the flat type seal, and its surface is a smooth plane, and it can also be machined with dense waterline. The sealing surface has a simple structure, is convenient to process, and is convenient for anti-corrosion lining. However, the contact area of the gasket on the sealing surface is large, and the gasket is easy to squeeze to both sides during pre-tightening, and it is not easy to be compressed.
Concave-convex type is a matching concave and convex sealing surface. It is convenient for centering during installation and prevents the gasket from being squeezed out. However, the width of the gasket is larger, and a larger pressing force is required. Suitable for occasions with slightly higher pressure.
The tongue and groove surface type is a sealing surface with matching tongue and groove surfaces. The gasket is placed in the groove and will not be squeezed out due to the obstruction of the groove. The gasket is relatively narrow, so the bolt force required to compress the gasket is correspondingly smaller. Even if it is used in places where the pressure is high, the bolt size will not be too large. Easy to center during installation. The gasket is evenly stressed, so the seal is reliable. The gasket is rarely eroded and corroded by the medium. It is suitable for important seals with flammable, explosive, toxic media and high pressure. However, it is difficult to replace the gasket, and the cost of the flange is relatively high. In addition, the tenon part is easy to damage, so care should be taken during disassembly or transportation.
O-ring face type This is a newer form of flange connection. It has a matching convex surface and a sealing surface of the groove surface, and an O-ring is embedded in the groove. O-ring is a kind of squeeze type seal. Its basic working principle is to rely on the elastic deformation of the seal to cause contact pressure on the sealing contact surface. When the contact pressure is greater than the internal pressure of the sealed medium, no leakage will occur, and vice versa. A leak has occurred. The process of using the medium itself to change the contact state of the O-ring to achieve sealing is called "self-sealing". The sealing effect of O-rings is more reliable than ordinary flat gaskets. Because the cross-sectional dimensions of O-rings are very small, light weight, less material consumption, simple to use, easy to install and disassemble, the more prominent advantage is that O-rings have good sealing capabilities, a wide range of pressure applications, and static The sealing working pressure can reach more than 100MPa, and the applicable temperature is -60~200℃, which can meet the requirements of various media.
Ring connection surface type, the flange of the ring connection surface seal also belongs to the narrow surface flange, and a ring trapezoidal groove is opened on the flange surface as the flange sealing surface, which is the same as the tongue and groove surface flange. The flange must be separated in the axial direction during installation and disassembly. This sealing surface is specially matched with solid metal gaskets processed with metal materials into an octagonal or elliptical cross-sectional shape to achieve a sealed connection. Because the metal ring gasket can be selected according to the inherent characteristics of various metals. Therefore, the sealing performance of this sealing surface is good, and the installation requirements are not too strict. It is suitable for high temperature and high pressure working conditions, but the processing accuracy of the sealing surface is relatively high.
Gasket
The gasket is a circular ring made of a material that can produce plastic deformation and has a certain strength. It is used for the sealing connection between pipelines and the sealing connection between parts of machinery and equipment.
Most of the gaskets are cut from non-metallic plates, or made by professional factories according to the specified size. The materials are asbestos rubber sheets, asbestos sheets, PTFE sheets, polyethylene sheets, etc.; there are also thin metal sheets (white iron sheet, Stainless steel) metal-clad gasket made by wrapping non-metallic materials such as asbestos; there is also a spiral wound gasket made of thin steel tape and asbestos tape. The most commonly used is stainless steel tape and graphite winding. Asbestos can also be used for spiral wound gaskets according to different use environments.
Ordinary rubber gaskets are suitable for occasions where the temperature is lower than 120°C; asbestos rubber gaskets are suitable for occasions where the temperature of water vapor is lower than 450°C, the temperature of oil is lower than 350°C, and the pressure is lower than 5MPa, and it is generally corrosive. The most commonly used medium is acid-resistant asbestos board. In high-pressure equipment and pipelines, metal gaskets of lens type or other shapes made of copper, aluminum, No. 10 steel, and stainless steel are used. The contact width between the high-pressure gasket and the sealing surface is very narrow (line contact), and the processing finish of the sealing surface and the gasket is relatively high.